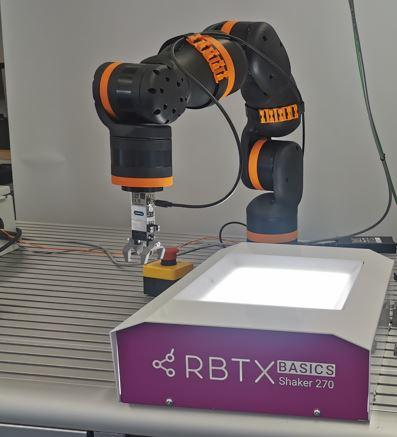
Pick and Place customer application with RBTX vibratory feeder and ReBeL cobot
Test Before Invest
Hardware Price:
easy to
integrate
DOF
6
Precision
+- 1 mm
In this customer application, plastic parts needed to be sorted correctly using vibration so that they could be recognized by a camera and picked up by a robot through coordinate transmission. This was necessary to ensure precise and efficient handling of the parts. The RBTX Varioshaker lite, a cost-effective product designed for simple applications from the RBTX range, was used in this example.
The Varioshaker lite was combined with a Rebel robot, an ifm 2D camera, and a Schunk EGP 25 gripper. The ifm 2D camera captured the position of the sorted plastic parts and transmitted the coordinates to the Rebel robot. The robot then used the Schunk EGP 25 gripper to precisely pick up and process the parts. This combination provided an efficient and cost-effective solution for the automated handling of plastic parts.
4 Components